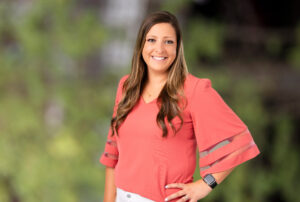
Image credit: Swinerton
In this series, Healthcare Design asks leading healthcare design professionals, firms, and owners to tell us what has their attention and share their ideas on the subject.
Carly Morris is the healthcare market lead at national construction firm Swinerton (Charlotte, N.C.).
Here, she shares her thoughts on states’ changing Certificate of Need regulations, using mass timber to address sustainability goals, and the impact of prefabrication on healthcare construction.
- Impact of CON changes on behavioral health design
The need for behavioral health beds has increased significantly, driven by rising mental health problems, population growth, COVID-19, the opioid crisis, and reduced stigmatization surrounding mental health. While Certificate of Need (CON) regulations help ensure quality and strategic planning, control cost, and coordinate resource allocation, they can also restrict access and availability, limit competition, slow the response to emerging needs, and become a barrier to entry for healthcare systems.
More than one-third of U.S. states have CON requirements of various types, but that’s starting to change. Recently, North Carolina and South Carolina reformed their CON programs that affect what healthcare facilities can be built or expanded, which in turn affects patient access to care and the cost of care.
The Carolinas’ revisions are sparking change across the country, with states such as Kentucky, Alaska, Vermont, and Minnesota currently reforming their regulations.
This trend is driving new behavioral health groups to enter the region due to the reduced barriers of entry and the opportunity to meet the demand for more new facilities.
With the recent reforms, the Carolinas are now ready to embrace partnerships that can address behavioral health needs and in turn decrease patient cost. Will other states continue to follow suit?
- Expanding flexible room capacity
The buzz among healthcare experts is about the value of flexible and universal hospital rooms to maximize available space. However, as healthcare systems struggle financially, the trend is taking another turn.
Many hospitals are also recapturing space by moving services that do not require a 24-hour stay, such as imaging centers, ophthalmology, and elective surgeries, to off-campus locations, some to suburban areas where real estate costs may be less.
Outfitting this now-available space with adaptive, universal rooms can offer cost efficiencies for health systems, who can buy in-bulk raw building materials (including flooring and wall protection), prefabricated headwalls, bathroom pods, and furniture and deploy the same layout from room to room.
- Impact of prefabrication on healthcare construction
While a standard practice on the West Coast, prefabrication is in the early adoption phases on the East Coast. The process promises increased quality control, accelerated speed to market, and consistent products.
Prefabrication solutions in healthcare include everything from building materials like the exterior skin to entire bathroom pods or segments of an emergency department.
The practice also adapts to the challenges posed by the construction workforce shortage by minimizing on-site fabrication with the associated safety and weather considerations and providing a more predictable work environment.
- Debunking the myth of mass timber
Mass timber reduces embodied carbon in the environment by as much as 75 percent. However, health systems are often hesitant to utilize wood in a healthcare setting, assuming that it cannot provide a sterile or easy-to-clean environment.
But more organizations are starting to see its potential. Swinerton’s first mass timber healthcare project includes a medical office building (MOB) in Virginia (the project is expected to move from design phase to development soon).
Swinerton’s team is currently conducting proof-of-concept studies to research the infection-fighting properties of wood. The goal is that this research will inspire more healthcare systems to look at mass timber to fulfill their pledge to reduce greenhouse gas emissions by 50 percent by 2030.
- Collaborative project delivery
Like prefabrication, operators, including those on the East Coast, are increasingly recognizing the benefits of early and ongoing collaboration on healthcare construction projects. Due to the complexity of these builds, particularly when a campus is open and operational, a design-build approach involves all invested parties from the design phase onward to minimize conflicts, clarify the vision, and set clear metrics for success and conditions for satisfaction.
Engaging stakeholders, contractors, architects, engineers, and major trade partners uncovers challenges, avoids pitfalls, and streamlines the process, ultimately delivering a facility that meets the intended use, budget, and schedule.
Want to share your Top 5? Contact Managing Editor Tracey Walker at [email protected] for submission instructions.